How to avoid the poor gloss on the molded plastic part surface?
What is the poor gloss?
Poor gloss refers that the molded plastic part does not stick to the mold, that means poor replication.
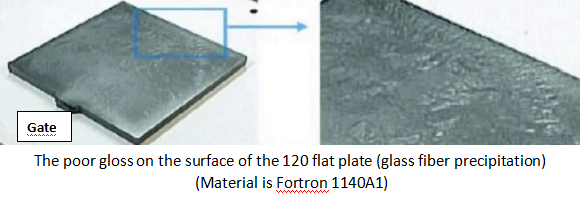
The cause of poor gloss
(2-1) It is caused by jetting mark or cold slug well.
When jetting mark or cold slug well appears on the plastic molded part surface, it looks like fog because it is different from the surrounding area. It often appears near the gate and in the uneven place.
(2-2) It is caused by the air.
The gas is blocked between the mold and the resin, which interferes their sticking on each other, resulting in poor gloss. It is more likely to occur when the holding pressure is low or the venting is not smooth.
(2-3) It is caused by the insufficient pressure.
Poor gloss is caused by the weak extrusion of the resin on the mold surface due to low pressure. The poor gloss is particularly obvious in materials containing fillers such as glass fiber, because the filler is easy to float to the surface and the resin is easy to sink inside.
For example, when the injection speed is low, the pressure cannot be transmitted to the end due to the resin solidification, which easily causes poor gloss at the end of the molded plastic part. At the same time, when the mold temperature is low and the overall solidification speed is fast, it is easy to appear the poor gloss of the molded plastic part.
How to deal with the poor gloss?
(3-1) Try to increase the holding pressure
First, try to increase the setting value of the holding pressure and the holding time. By this way, it is showing a tendency to improve. If not, the actual insufficient pressure rise in this part may be caused by other reasons.
At this time, the following countermeasures should be used simultaneously:
(1) Increase the mold temperature
(2) Increase the barrel temperature, specially for the nozzle
(3) Increase the gate size
(4) Increase the injection speed
(5) Use a material grade with good fluidity
In this way, it is expected to get good results in terms of mold temperature and gate size.
(3-2) Check the vent
It is necessary to check whether the gas has been vented. Check whether the vent thickness and size required for effective exhaust of gas, whether it is contaminated by mold deposit, etc. It is also important to configure it in the appropriate position. If possible, it is recommended to use the short shot method to understand the actual resin flow condition.