Problems & Solutions of The Production Mold
When the production mold is in the production process, it may meet various problems, which can affect the quality and production efficiency of the product. We would like to share with you some common problems & solutions of the production mold.
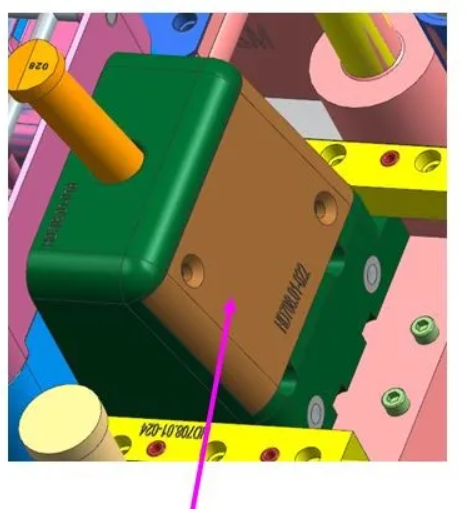
Problem 1: Unstable Dimension
The dimension of the plastic part is unstably change because the strength and precision of the mold are poor, injection molding machine operation and molding conditions are unstable.
Solution 1: It is necessary to improve the manufacturing precision and strength of the mold, while ensuring the stability of the injection molding machine and molding conditions.
Problem 2: Excessive flash
Due to poor mold closing and too large gap, and the excessive plastic fluidity or material addition, the plastic part is extruded excessive materials along the edge.
Solution 2: It need to adjust the mold closing gap, reduce the feeding amount and optimize the injection molding parameters.
Problem 3: Poor welding
The material temperature is low when the molten material is divided and merged, the resin and the attachment are incompatible, which will cause the poor welding.
Solution 3: It can be improved by increasing the material temperature, optimizing material selection and mold design.
Problem 4: Wave marks on the part surface
The molten material does not flow neatly along the mold surface to fill the cavity, but flows in a semi-solidified wave shape on the cavity surface or the molten material has viscous flow.
Solution 4: Optimize the mold design and injection machine parameters to ensure smooth flow of the molten material.
Problem 5: Poor demoulding
Due to excessive filling and poor mold demoulding performance, the plastic parts are difficult to demould or deformed and cracked after demoulding.
Solution 5: Improve the demoulding design of the mold, use appropriate release agent and optimize the injection speed.
Problem 6: Layering and peeling
Due to the foreign materials or low mold temperature, the shearing effect is too large when the molten material flows along the mold surface, resulting in the material layered to peel off and the physical properties to decrease.
Solution 6: Ensure the consistency of the material and control the mold temperature.
Problem 7: Gate sticking to the mold
Due to mechanical resistance in the gate sleeve, insufficient cooling or failure sprue puller, the gate sticks to the gate sleeve.
Solution 7: It can be solved by improving the mold design, ensuring the effectiveness of the cooling system and checking the function of the sprue puller.
Problem 8: Poor transparency
①Poor contact between the molten material and the mold surface; ②Small pits on the plastic part surface cause light to radiate randomly; ③Plastic decomposition; ④Foreign material and impurities; ⑤The mold surface is not glossy. Therefore, the transparency of the transparent plastic is poor or uneven.
Solution 8: Improve the quality of mold surface treatment, optimizing material drying and injection molding parameters.
Problem 9: Silver streaks
①Moisture or air in the material; ②Excessive volatiles; ③Excessive shearing of the molten material; ④Poor fit between the molten material and the mold surface; ⑤Rapid cooling of molten material; ⑥Mixing with foreign materials or decomposition and deterioration. Therefore, the plastic part surface will appear sliver streaks along the material flow direction.
Solution 9: Optimize drying and injection parameters, ensure the cleanliness of the mold surface, and control the drying of the material.
Problem 10: Warping & deformation
Firstly, it will cause the internal stress due to residual stress, shear stress, cooling stress, and uneven shrinkage during forming. Secondly, it is appeared poor demolding, insufficient cooling, insufficient strength of the plastic part, mold deformation, etc. Under the above cases, the plastic part will have deformation, uneven warping, uneven mold holes, uneven wall thickness, etc.
Solution 10: Optimize mold design, adjust injection and cooling parameters, and perform mold flow analysis to predict and reduce warping.
Problem 11: Cracks
Due to excessive internal stress in plastic parts, poor demoulding, uneven cooling, poor plastic performance or poor plastic part design, cracks are generated on the plastic parts surface and near the feed inlet.
Solution 11: Optimize design, adjust injection molding parameters, and ensuring sufficient cooling and annealing.
Problem 12: Black spots or black stripes
Under high temperature and high pressure, the decomposition of plastic, flammable volatiles and air in the material, are decomposed and combusted, and then the combustion products are injected into the cavity along with the molten material, and black spots, black stripes and burns appear on the plastic parts surface.
Solution 12: Optimize material processing, ensure the cleanliness of the mold and barrel, and adjust injection molding parameters.
Problem 13: Short shot
Mainly due to insufficient feeding, poor fluidity of molten material filling, excessive inflation and poor exhaust, it will cause the short shot of the plastic parts.
Solution 13: Optimize injection parameters, ensure sufficient feeding and improve the exhaust system of the mold.
Problem 14: White mark on the product surface
This is mainly due to insufficient cooling time or too fast ejection speed, unbalanced ejection force, resulting in ejector marks on the product surface.
Solution 14: Adjust the cooling time and ejection speed, and optimize the ejector pin design.
By identifying and solving these problems, it can improve the stability of the production mold and the consistency of products, thereby improving production efficiency and product quality.